
Forensic Science Northern Ireland (FSNI) is an Agency within the Department of Justice, responsible for the provision of impartial scientific advice and support, to enhance the Criminal Justice System.
FSNI currently employs approximately 200 staff, all civil servants, of whom roughly 65 per cent are scientists directly involved with casework.
A Personal Perspective from the View of the Leader
This Study takes the form of an interview…
Derek Kennedy talks to Catalyst about his experiences with Lean Six Sigma during his time at FSNI – Unique challenges presented by a team working on on sensitive topics. What do a team of forensic scientists have in common with a family of ducks?
Lean Six Sigma, Why did you start it – what prompted you to get going?
Derek – Context…
Society in Northern Ireland had normalised, and crime associated with the “Troubles” had diminished. Crime trends are now more like those elsewhere in the UK with similar populations. Forensic Science Northern Ireland (FSNI) had to be both accurate (which it always was) but without the luxury of time (it always had as much as it wanted) in order to meet societies expectations and those of the NI criminal Justice system (CJS). The Judiciary were demanding that the speed of the forensic activities be improved as a justice system awaited results from forensic analysis that traditionally was afforded all the time it needed to get the results correct. The Police Service Northern Ireland working now under new budgetary pressure demanded that forensics be commercially competitive with the private forensic market elsewhere in the UK, effectively demanding value for money. The Department of Justice (DoJ) above all had to ensure that the confidence in the justice system was never compromised while working within a new budgetary environment that was never before imposed on Northern Ireland.
We had to address the urgent need to achieve results with the same or diminishing resources. In effect, we had to succeed with what we had or with less than we had (both money and people) and we needed a methodology that would protect the effective portions of our processes and not compromise on the quality of our science. You can imagine the paramount importance of maintaining quality during a period of reform in a Forensic Environment within a criminal justice system such as Northern Ireland. In short, change was urgently required as the people of Northern Ireland expected more, and the Exchequer expected us to do it with less.
Before you started what did you think / what previous experience had you had?
Before we started I avoided Lean Six Sigma like the plague. I had studied it during my post grad but promptly discarded it as something that would benefit manufacturing, not service or public sectors. I had a breadth of experience in continuous improvement activities and was certain that the appropriate tool for effective change would emerge naturally as I understood the organisation better. In regards to Lean Six Sigma, I wanted to discard it as an option…but something niggled me about it.
The reliance on data within the methodology sat well with me and the culture within the forensic environment. As much as I wanted to, I knew it might have a part to play. Then having been invited to go to the Netherlands national Forensic lab to see how they approached a similar challenge I arrived to find them in the second year of their Lean Six Sigma journey and the thing I wanted to dismiss became apparent as the correct tool for us as it was already proven to drive results in a forensic environment.
With my own cognitive bias overcome, I realised it was “hard to kick against the goad”, and that Lean Six Sigma was the perfect fit for FSNI. In fact, I was determined to use a methodology that fit best with the culture of the organisation and to that end I expended a considerable amount of time and effort to understand the culture to find that Lean Six Sigma sat perfectly as the right tool to produce sustainable results.
How did you get started?
Imagine a team of ducks who have lived their natural lives for the past 21 years on a river because the pond they enjoyed over 20 years ago was destroyed by a man made disaster. Having been used to the consistency of the former pond they had been thrown into a new river, a new and strange environment. Daily they live their lives at any one time swimming against the current or indeed with it. Needless to say the effort required to just swim in any one day was considerable. Challenges around keeping the young ducklings safe, and teaching methods on how to survive on the river got passed down through the generations of ducks, all the time the memory of the old pond became talked about in legend and songs. How did I start? I wanted to know how the ducks functioned, thought and felt about their environment, what they believed was possible, did they fly, if so how far were they willing to go?
I got started by clearly understanding the culture of the organisation. One of our goals was to improve the culture in a real and meaningful way. If we were to improve the culture in FSNI then it had to, at the end of our journey, be tangible, visible and felt. My fear was that words like culture are often (over)used in the workplace but never clearly defined, hence we defined culture. For the purposes of our Transformation it was imperative that FSNI defined the existing culture in order to move towards a further improved state. For our purposes, we defined culture as noted by Edgar Schein an accepted foremost expert in organisational culture. He formally defined culture as;
“the pattern of shared basic assumptions that was learned by a group as it solved its problems of external adaptation and internal integration, that has worked well enough to be considered valid and, therefore, to be taught to new members as the correct way to perceive, think, and feel in relation to those problems”
I had observed culture at the various levels within FSNI, and by assessing FSNI’s cultural Artefacts, Espoused Beliefs and Values and Underlying Assumptions that existed within the organisation was able to better understand what improvement methodologies might me most effective. They were defined as;
Key Cultural Artefacts (the visible organisational structures and processes) discovered were:
- FSNI was located in a disused tobacco factory.
- FSNI is based in a very litigious and adversarial Criminal Justice System
Espoused Beliefs and Values (the strategies, goals, philosophies and espoused justifications). This is in the context of the impact of the preceding 21 years after the Lab was blown up and the staff were promised a new lab…In the meantime they carried out the highest standard of science from what was supposed to be a temporary solution for 21 years after the Newtownbreda Bomb) They were;
- The belief existed that the environment staff worked in was not important to senior management and a new Lab was not a priority for them.
- The belief existed that stakeholders within the CJS were not be able to move at the same pace of change as FSNI and as a result would become a barrier to change in FSNI.
- The CJS did not facilitate or want change.
- FSNI as an organisation believed it had to continually defend their position.
Underlying Assumptions (the unconscious, taken for granted beliefs, perceptions, thoughts and feelings of groups or individuals which form the source of their values and actions).
- The new Lab would never happen
- Change in general and changes in processes would be limited
- Even if change did happen it would have a very limited impact
- FSNI senior management and the DoJ did not care about the work environment or the quality of the science of the FSNI team.
So what does this have to do with Lean Six Sigma?
This meant that we were not simply forcing the organisation to adapt a new methodology, but rather we were developing a new way of working that best fit with the way they already operated, as well worked to reduce the impact of the negative aspects of the existing espoused beliefs and underlying assumptions by aligning the approach with the culture of FSNI.
Back to the Ducks
Effectively what I am saying is that scientist took to the data driven approach offered by Lean Six Sigma like ducks take to water. While I would not say it felt natural to them, I knew that if they could find a way to exert the same or less effort in an environment that was familiar to them they might just see that ducks don’t have to just live on a river…there were other waters available to live on.
What were you trying to achieve ?
Hard Deliverables
- More for less (15% improvement in time and 10% reduction in costs)
- Culture Change (tangible, visible and felt)
Soft Deliverables
- Less tired ducks
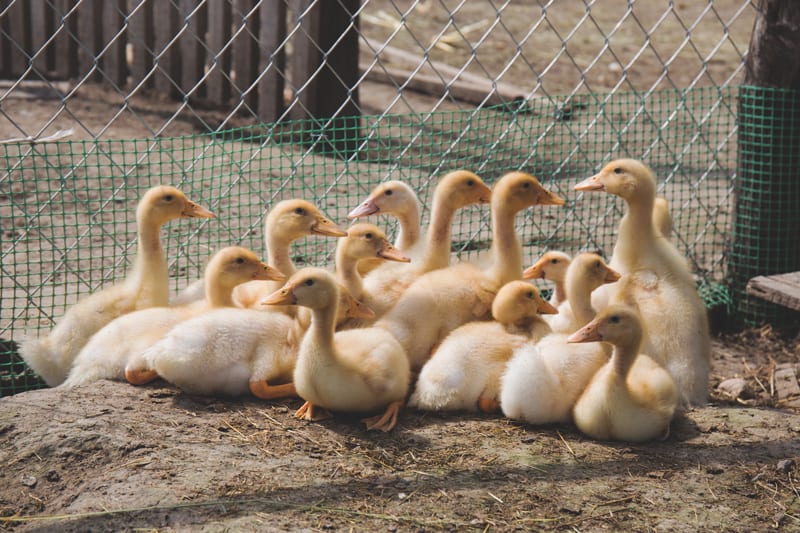
How did you go about it?
Started with the culture, then developed a change management strategy based on Kotter’s 8 Steps (Now using Kotter’s XLR8). I ensured the Change Management strategy had real hard actions designed to start, sustain and maintained the changes (48 actions to be exact all with timescales, ownership and accountability assigned…no easy feat in a public sector environment).
Then we needed to train ourselves in Lean Six Sigma…we had to become the new way of working. We selected a world class partner to assist us and we picked who we thought were the best suited ducks for the challenge. Some ducklings were suited to yellow belt training, others were already flying and could really use the tools a greenbelt would have. Some ducks we mistakenly gave the training to who should have just focused on their important roles in the team and not Lean Six Sigma. One duckling just stood out…there was something special about her, she could relate to all the other ducks but also speak with authority to the Big Flockers. She never wavered, trusted the direction and the methodology and the data that came out of it and stuck to it. She also had a good friend who did not come from the river. A strange bird that migrated from somewhere in French speaking Europe but that did not matter because everyone was able to understand her. She was able to inject energy, and hope that a better way of living was within our grasp.
We never gave up. There were times when the needs of the CJS would have led you to believe that there were other things more important but we were relentless. No matter what came against us we just kept going…Define, Measure, Analyse, Improve, Control, Define, Measure….
What were the biggest barriers?
- We learned that not everything that swims on the river is a duck…we had to deal with some cormorants, who insisted they were ducks but they always seemed to be disappearing under the surface (where did they go? what were they doing and who exactly were they talking to down there because their data never seemed to completely add up).
- Celebrating success in the environment of public sector austerity was challenging.
- The constant tension between business as usual and the need to change was at times hard to manage.
- The top level of middle management…these are the ducks who are tasked with the doing of BAU and the leading of the change…and some of them just would not get in the water. They thought their role was to quack loudly from the river bank but never actually get wet.
What were the greatest successes?
- Drugs project (award winning)
- The reporting project sped everything up by nearly 50%.
- Lean Six Sigma made the organisation believe that it could change itself…that they were capable of solving the problems it faced…that more money and more people were not the solution to the problem.
- The Big Flockers learned that the tool while it could be very sophisticated (because we all know that Big Flockers like to be Big Sophisticated Flockers!) did not always need sophisticated solutions. Some very simple management actions as a result of the data could achieve remarkable results and improve the performance of individuals and teams with very little action required.
- Lean Six Sigma assisted to make the culture change tangible (something real we could attribute change too), visible (our performance was now transparent bringing accountability to teams and individuals) and felt (people started to enjoy their jobs and work environment again).
With hindsight, what would you do differently?
- I would have thought more strategically about the initial project selection. Our projects initially were selected using a bit of a scatter gun approach. As we became more confident in the methodology projects naturally emerged.
- The selection of capable greenbelts and yellow belts is critical. Don’t select any cormorants passing themselves off as ducks!
- Our special duckling…I would have had two of her…so she would have had more support. I know these are very rare and special ducks but if you listen to the entire team you will see there are a few special ducks and when you get them working together it offers each of them support and builds in contingency and builds the confidence of the Big Flockers looking for results.
What advice would you give to other leaders?
- UNDERSTAND THE CULTURE OF THE ORGANISATION!!! USE IT AS A LEVER TO ENSURE SUSTAINABLE CHANGE.
- Have a strategy…not just a plan. If you only have a plan and it goes pear shaped how will you know what direction to continue in? A strategy acts as a compass in the stormy environment of change and lets you know if you are making progress when you are too close to the detail.
- A lot of little wins can seem insignificant but don’t worry, they can and will soon add up to an overall significant change.
- Not all projects will yield something…don’t fret…keep going.
- Choose your team carefully.
- Find a special duck or two.
- You live under a microscope…everything you say and do is recorded and will be played back to you by people in the organisation. You need to live what you are talking.
- Get someone outside the organisation to support you…it is lonely and you will need someone to encourage you…like the strange European bird or a wise welsh owl.